Products and services for hydrostatic components & systems
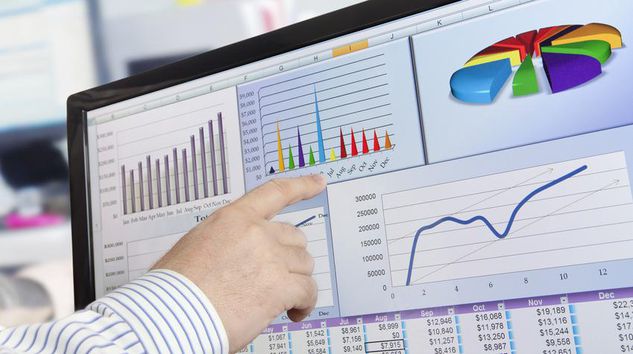
Engineering services for hydrostatic components
For rather slow movements where higher viscosity oils corresponding to VG 22 to approx. VG100 can be used, as is the case with linear guides and slowly rotating rotary tables, for example, we offer our customers engineering services to determine the dimensions and technical data of hydrostatic components, usually taking our PM controllers into account. Customers then receive a drawing with the required hydrostatic pockets and all the dimensions of the hydrostatic pockets.
PM controller for guides
Optimum dynamic conditions are achieved when the line between the PM controller and the hydrostatic pockets is very short.
For this reason, the attachment controller was developed, which is used, for example, with hydrostatic screw drives and with spindle bearings. But can also be used for guided tours.
These attachment controllers are usually attached to a flat ground surface of a machine part with hydrostatic pockets in such a way that the connection from the central connection of the attachment controller to the hydrostatic pocket is achieved only through a hole that is as short as possible.
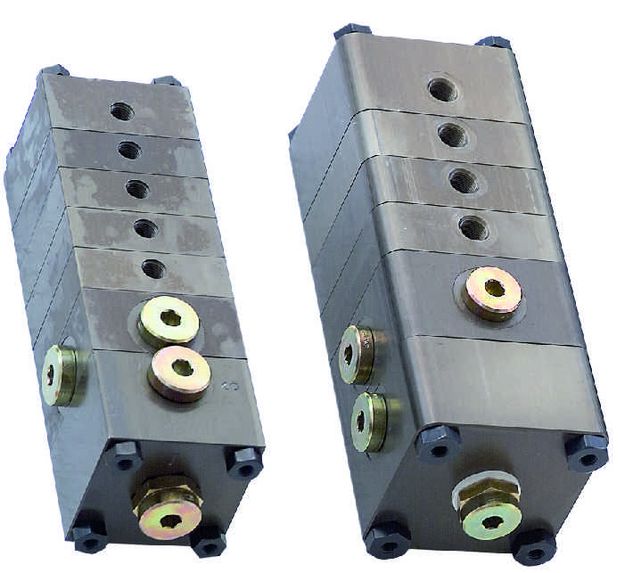
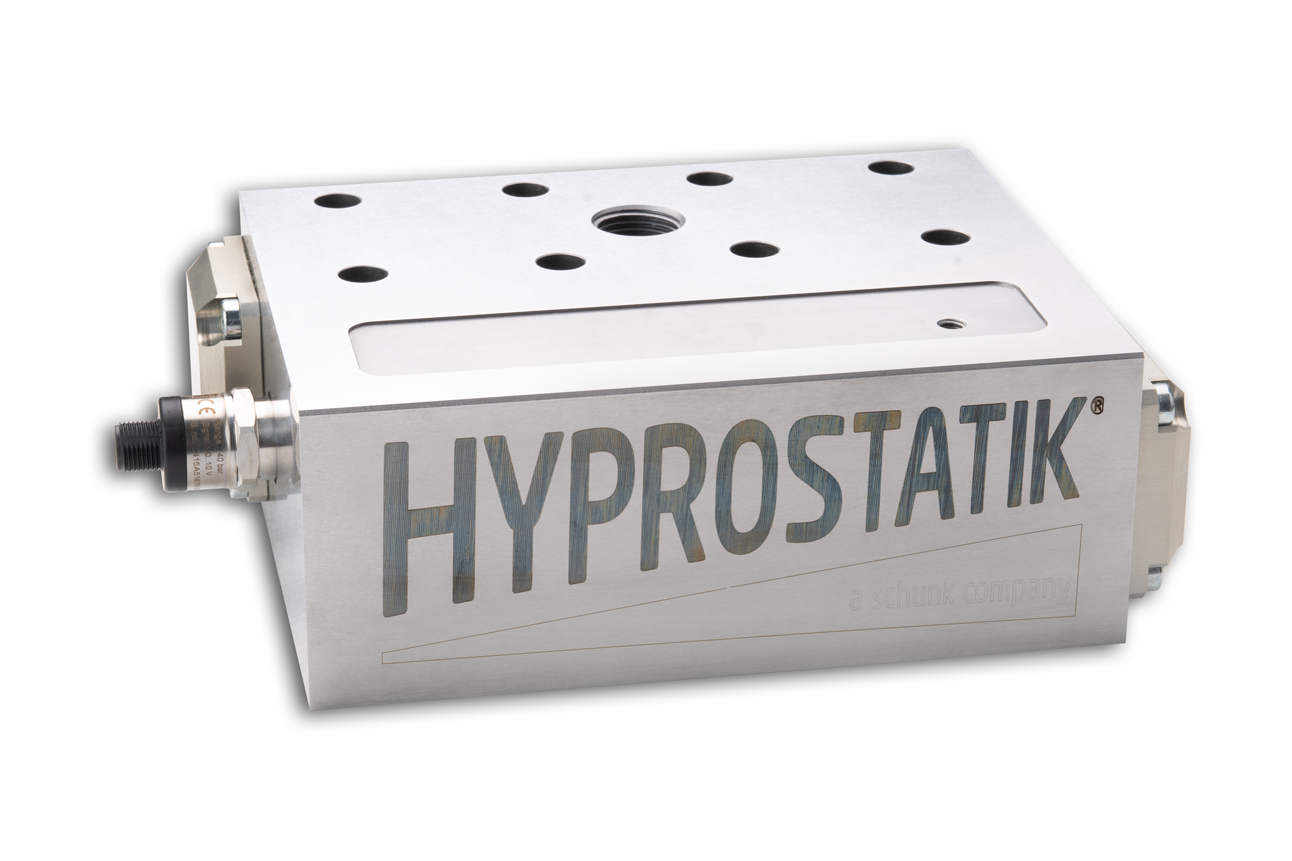
Hydrostatic guides
Our guide shoes are available in two variants: the symmetrical design is suitable for narrow guides. The asymmetrical design is perfect for wide guides and ultra-precision machines. Of course, special designs are also possible for very special applications. In addition, other cross-sectional profiles and circular-ring segments for rotary tables can also be realized.
A clamping element can be inserted between the guide shoes on both sides. This element has a screwed-on bronze element, which can be applied to the guideway in the middle diaphragm area via an adjustable pressure. The clamping element can be used to add damping or friction in the direction of movement of an adjustable magnitude if this is helpful for machining.
Hydrostatic lead screws & bearings
Advantages over the ball screw and rolling bearing at a glance:
- Wear-free, as there is no contact during operation
- no loss of accuracy, even in long operation under full load at maximum
- Speed
- frictionless at low speeds
- No reversal of the frictional force when changing the direction of rotation
- Transmits the slightest rotary movements
- No stick-slip effect even at low speeds
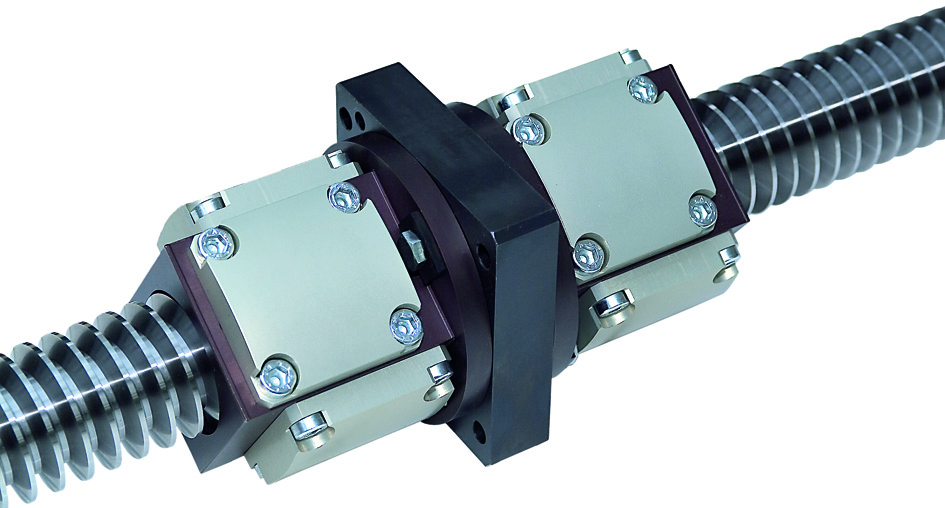

Hydrostatic bearing
Advantages of hydrostatic spindle bearing arrangements HYPROSTATIK® system
- Wear-free and thus service life-independent properties
- exceptionally high runout and axial runout quality
- High static as well as dynamic radial and axial stiffness
- exceptionally high damping
- Low friction and pump power due to our patented PM controller and optimal design by means of comprehensive calculation programs
- Minimal temperature variation of a few °C due to suitable oil cooling and thermal insulation between motor and spindle bearings
- excellent balance quality
Hydraulic power units
Technical data:
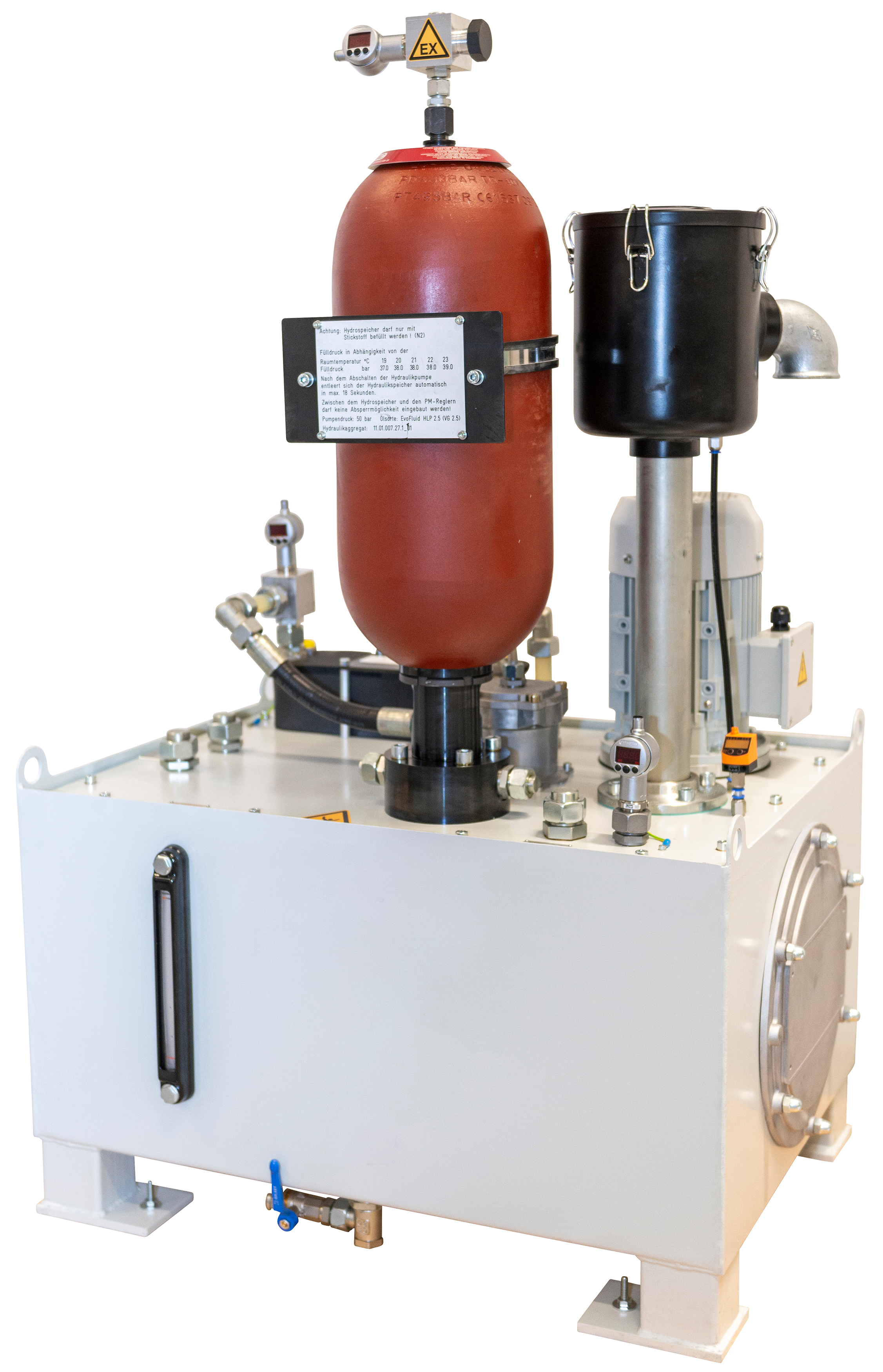