HYDROSTATIC GUIDES – ADVANTAGES OF HYDROSTATIC GUIDE SHOES
Wear-free
-
- Unlimited service life
- Properties of the machine do not change with the service life
No friction at standstill – no stick-slip effect
-
-
- Positioning accuracy is not limited by the guide
- Very small travel steps and very slow movements possible
-
Excellent damping, no vibration
-
- improved surface
- vibration-free running
- very high load capacity due to large pockets
- Very high stiffness due to PM controller
- an oil inflow with constant pressure
- integrated flow control
- Attached pressure sensors for monitoring the preload and external loads from CNC
- low deformations due to screws
- simple construction of the surrounding parts
- select the pump pressure 32, 50 or 80 bar according to your max. Loads
- select oil viscosity VG32, V46 or VG68 according to your max. Speed
Our hydrostatic guide shoes are available in two versions: the symmetrical design is suitable for narrow hydrostatic guides. The asymmetrical design is perfect for wide hydrostatic guides and ultra-precision machines. Of course, custom-made hydrostatic guideways are also available for very special applications. In addition, other cross-sectional profiles and circular-ring segments for rotary tables can also be realized.
A clamping element can be inserted between the hydrostatic guide shoes on both sides. This element has a screwed-on bronze element, which can be applied to the guideway in the middle diaphragm area via an adjustable pressure. The clamping element can be used to add damping or friction in the direction of movement of an adjustable magnitude if this is helpful for machining.
3 HYDROSTATIC GUIDES AT A GLANCE
11 Advantages of using PM controllers on hydrostatic guideways
- Often, a wrap-around can be omitted if the load directions allow it, since with PM controllers the wrap-around is often not necessary only to increase the stiffness
- In the case of hydrostatic guideways without a grip, the rigidity can also be significantly increased using vacuum pockets
- The stiffness of the hydrostatic guideway can be adjusted largely independently of the load capacity by varying the preload on hydrostatic guideways with grip
- No wear with increasing service life
- Damping improved by orders of magnitude, resulting in significantly better workpiece surface and tool life
- No vibrations and fluctuations in friction as with rolling guides due to recirculating balls
- No reversal jump of the feed force when reversing the direction of movement
- Virtually frictionless at low speeds
- No stick-slip effect
- Travel smaller than 0.1 µm possible
- Sliding properties of the materials, the carriage and the guideway are insignificant, mineral casting, aluminum or impression compound can also be used
Adaptation of the hydrostatic guide to:
- Weights, machining and acceleration forces
- Maximum speed and acceleration as well as desired stiffness and optimum damping
Open guide
Open hydrostatic guide – Advantages
- Hydrostatic guidance with highest precision and excellent stiff directional guidance for horizontal applications, provided machining and acceleration forces on the pockets are significantly smaller than the weight forces
- Preload can be increased by means of weights using vacuum pockets (shown in dark orange) Particularly suitable for cylindrical grinding, surface grinding and workpiece axes of large milling machines
V-face guide
Hydrostatic V-surface guide – Advantages
- No deformation due to screws, thus highest precision
- Low manufacturing costs, since no surfaces have to be ground to size and no ledges are necessary for horizontal applications, provided machining and acceleration forces on the pockets are significantly smaller than the weight forces
- Increase of preload and thus stiffness possible by means of vacuum pockets (shown in dark orange)
- suitable for cylindrical grinding, surface grinding, measuring and ultra-precision machines
- the stiffness of the directional guide increases with load on the V-track
Perimeter guide
Hydrostatic handle guide – Advantages
- For guideways with loads in any direction, i.e. also lifting forces
- easy to manufacture, highly accurate and extremely parallel vertical hydrostatic gaps
- low manufacturing costs, since no part has to be ground parallel and to size
- the size of the vertical sum gap is determined by a step grind on one side of the two handle bars
- for horizontal and vertical slides with large forces, moments and high stiffness
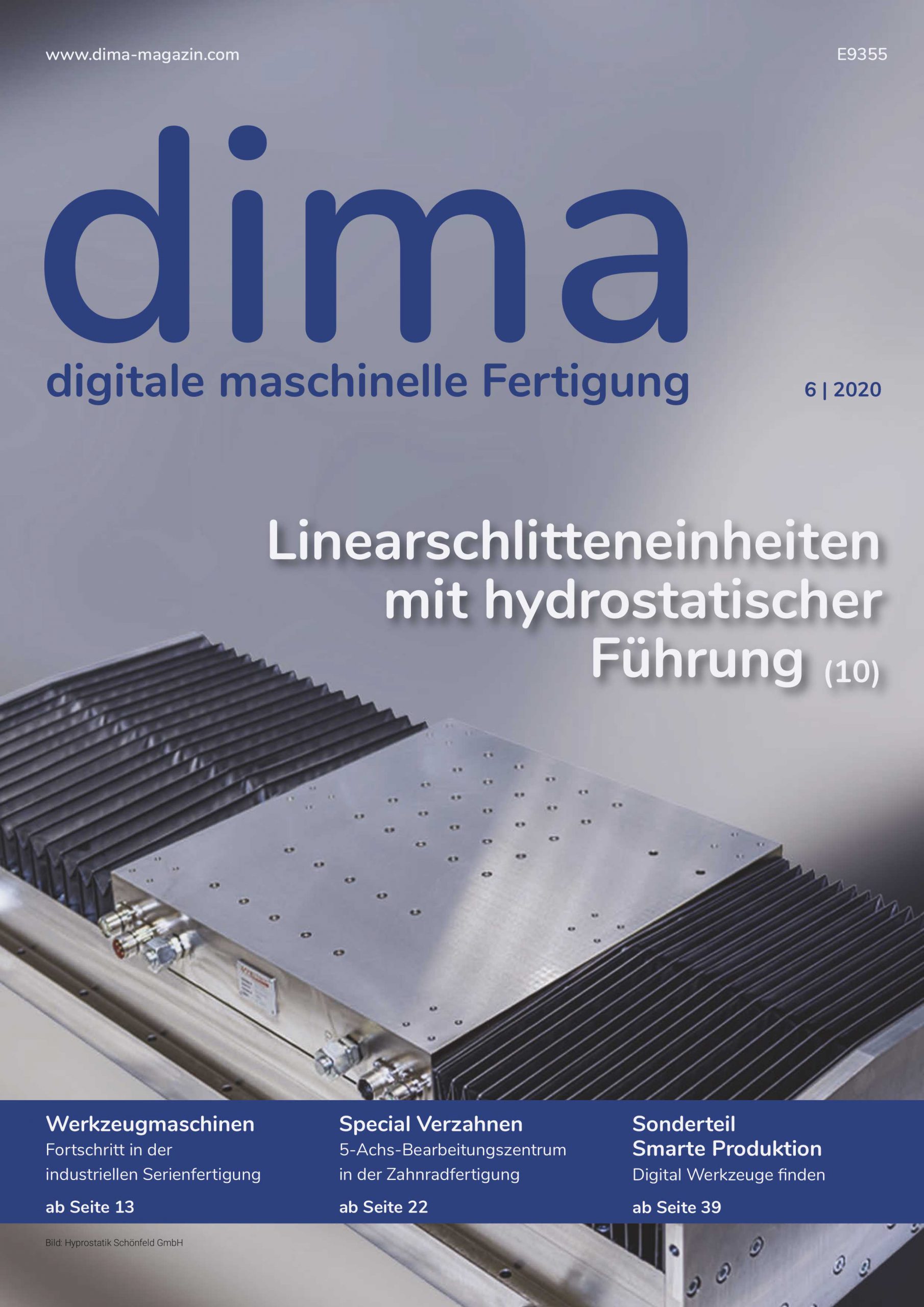