TECHNOLOGY
It’s the position that counts – Innovative progressive flow regulator from HYPROSTATIK
Almost everyone is familiar with the decorative spectacle that can sometimes be seen in front of large buildings: a heavy stone or metal ball rotates almost frictionlessly in a half shell. The reason for this comes from below – water pressure, generated by a pump, lifts the ball and makes it float on a film of water with virtually no friction or contact with the shell. A hydrostatic water film.
Less appealing to look at but just as effective, this method can be used to support moving machine parts: Since the moving parts do not touch each other, there is no wear. Refined by our innovative progressive flow controller and sound advice, the high-quality HYPROSTATIK solutions make use of precisely this principle. To the benefit of our customers’ machine tools: They become more accurate, more reliable, more durable and more effective.
Advantages of progressive hydrostatics from HYPROSTATIK compared to “normal” hydrostatics from other suppliers
Calculation programs
Hyprostatik is the exclusive supplier of comprehensive and frequently tested calculation programs for the calculation and optimization of linear guides, spindle bearings, rotary tables, center bearings and special designs. With these programs, not only the data of hydrostatic components against static loads such as stiffness, load capacity, load reserve, friction and pump performance minimum gap size at maximum load …., but also damping values in dependence on the excitation frequency such as energy absorption capacity, vibration amplitudes …. can be calculated and thus optimized.
– The following hydrostatic components can be calculated and optimized:
–
Cylindrical hydrostatic radial bearings with definition of the bearing arrangement for a given radial bearing stiffness and a given maximum radial load
–
Hydrostatic thrust bearings also with two bearings acting against each other with definition not only of the axial stiffness and load capacity, but also of the moment stiffness and load as well as the skewing due to the given moment load as well as the minimum gap size at maximum moment load
– Complete spindle bearings with calculation of the bearing loads, the share of the front and rear bearings, the spindle part between the two radial bearings and the projecting spindle part in the radial compliance at the point of application of a radial load. Further the skew positions of the spindle in the two radial bearings, the optimum bearing distance or the data for a given bearing distance
– Rotary tables
The bearing arrangement of rotary tables usually consists of only one radial bearing and a “double” thrust bearing, which absorbs the axial and moment loads. Since we can also calculate the load capacity of a thrust bearing and its moment stiffness with our calculation programs, it is possible for us to define optimum rotary table bearing arrangements for specified radial, axial and moment loads as well as various speeds, including high speeds, and to specify the expected radial, axial and moment stiffness in addition to other data.
– Linear guides
For linear guides, we can also calculate individual pockets without a circumference using our calculation programs. Such pockets can only be used for guiding slides, which are held on the machine bed by their own weight. By means of our PM controllers, we often obtain high stiffness even without a handle. The stiffness of such slide guides can be doubled or increased several times without circumvention by means of large, fluid-flushed pockets between the hydostatic pockets, from which we draw fluid by means of a small jet pump, thereby creating a negative pressure of approx. 0.9 bar in these pockets. If, despite this, the stiffness is not sufficient or if lifting forces have to be compensated, guides with a handle, i.e. with two pockets acting against each other, are required. Computer calculation programs are also available for such pocket pairs, by means of which all relevant data are calculated against static and dynamic loading of such pocket pairs.
By means of these programs, with which all relevant data of hydrostatic components can be calculated with high precision, it is possible to design hydrostatic components optimally against static and dynamic loads (damping).
PM controller (progressive volume controller)
As far as we know, the PM regulators in their wear-free and hysteresis-free design, controlled purely mechanically only by the differential pressure between the inlet pressure (= pump pressure) and the outlet pressure (= pocket pressure), are only available to us.
This controller measures increasingly loaded hydrostatic pockets with a higher oil flow, but relieved pockets with a lower oil flow. The oil flow through the regulator therefore increases as the differential pressure across the regulator decreases, and decreases as the differential pressure across the regulator increases.
The regulator thus allocates a higher oil flow to more heavily loaded hydrostatic pockets and a reduced oil flow to pockets with lower loads.
This behavior is achieved by means of two throttling points in each regulator, one of which modifies the differential pressure across the second throttling point in the desired manner by means of an elastic, hysteresis and wear-free deformation, so that this desired behavior of the regulators is achieved.
Competitors usually apply capillaries instead of the regulator.
Stiff
The stiffness of hydrostatic components with capillaries is often insufficient. With our PM controllers, four to five times the stiffness of capillary solutions can be achieved. In many cases, this allows higher stiffnesses as with rolling elements and also guides without a handle. For decades, we have been offering a solution with vacuum pockets between the hydrostatic pockets, from which oil is extracted with a simple jet pump, generating a vacuum of approx. 0.9 bar, and in some solutions no handle is required. Also, due to this high stiffness, only we succeeded in developing and supplying a screw drive with a hydrostatically supported nut, which was measured by WBK Karlsruhe with double the stiffness between the nut and the screw shaft compared to ball screws of the same size.
The largest screw drive delivered so far is designed for 340 kN permissible load with a spindle diameter of 125 mm and is used in a broaching machine in Untertürkheim. The first of these screw drives was irreparably damaged after about 9 years, after which the control system of the machine failed and the motor demolished the machine. Its successor has been in use for about 7 years.
Wear-free
Hydrostatic components avoid contact between moving and stationary machine parts. This prevents wear, which achieves the following:
–
The components retain their function and precision unchanged over the entire service life, i.e. over years and decades
–
availability and productivity are increased
–
the useful life and service life are significantly extended
–
the downtime and maintenance costs are significantly reduced
Friction characteristics
– The frictional force is very small even for the heaviest machine parts and is strictly proportional to the speed. As a result, position errors are completely avoided, especially when the direction of movement of a linear slide is reversed, and drag errors are also virtually eliminated. Position errors of linear guides and rotary tables are thus largely avoided and the path accuracy of these components is very high.
–
Stick-slip is reliably avoided even under high loads
–
Slide drives are practically only to be designed for sufficient accelerations and machining forces and are therefore smaller and more cost-effective to define due to the negligibly low frictional force
Optimal damping
– The vibration damping of hydrostatic components optimized by us is generally an order of magnitude higher than that of rolling elements, in many cases several orders of magnitude higher, especially at low excitation frequencies.
Hyprostatik optimizes damping by means of its calculation programs, which means that the decisive “damping absorption performance” is ten times greater than that of non-optimized hydrostatic components.
– This becomes understandable when one knows that the damping force at higher excitation frequencies is proportional to the viscosity and the third power of the web width and inversely proportional to the third power of the gap height. The damping force can therefore be optimized to a very high degree by optimally selecting the web widths and gap sizes in particular.
–
High damping, i.e. better damping absorption performance, results in higher universality, since due to higher surface quality, damping and shape accuracy of the workpieces, wider use and possibly also hard machining is possible, since regenerative chatter is largely avoided.
Running quality and web fidelity
–
Due to the integrating effect of hydrostatics, errors of guideways which are shorter than the hydrostatic pockets are almost completely eliminated.
– Radial and axial running errors smaller than 0.1 µm are possible over the entire speed range, even at high speeds. Concentricity errors of 30 nm have already been delivered.
–
The running qualities remain unchanged over the entire service life due to the absence of wear.
Temperature stability
– By recooling the hydrostatic oil before it enters the machine, if possible slightly below the room or rack temperature of the machine, not only is heat input into the machine largely avoided, but the machine is also kept at a constant temperature. This makes it possible to dispense with thermosymmetrical design. This also almost completely eliminates heat drift after the machine is switched on.
–
This is also possible with very fast running spindle bearings.
– As a result, only a very small amount of heat is generated by the machine. If cooling is activated only when the steady-state temperature of the fluid has been reached, the already short warm-up phase is again greatly reduced
Further possibilities
–
By measuring the pocket pressures, it is possible to monitor the machine and the load limits and also, for example, to monitor tool wear.
– Furthermore, a cylindrical hydrostatic radial bearing allows both rotary and linear movements of the shaft in the bearing bore, so that (for example, as with a rotating tailstock sleeve) an additional linear guide can be dispensed with. This possibility does not exist with rolling bearings.
Advantages compared to rolling systems
Power of ten better damping
Your advantages:
- higher quality of the workpiece surface
- higher tool life and
- higher limiting cutting performance
Wear-free
Your advantages
- Machine characteristics independent of service life
- greater availability of the machines
- lower maintenance costs
- longer machine life and
- lower annual machine costs
Lower concentricity errors and higher precision of guideways
- Your advantage: higher workpiece accuracy
Very low and speed-proportional friction of the guideways
- Avoidance of path errors even when the direction of movement of slides is reversed,
- Avoidance of stick-slip effects and highest positioning accuracy and path fidelity even with very large slide weights and smallest paths even in changing directions.
No force or torque shocks due to roller deflections in guideways and screw drives
- higher surface quality and greater workpiece accuracy.
Reduced sensitivity to soiling
As contamination in hydrostatic bearings is mainly flushed out by oil and is not rolled into the raceways as is the case with roller bearings and guides, our customers benefit from the following:
- higher functional reliability
- Machine characteristics independent of service life
- greater availability of the machines
- lower maintenance costs and
- longer machine life and
- lower annual machine costs
Smaller installation space possible as the roller bearing parts are no longer required
Your advantages:
- Freedom in the design
- adjacent components can be dimensioned larger and
- smaller components become possible with the same conductivity.
Shape errors in the guide surfaces are largely compensated for by the hydrostatic system
Your advantages:
- Concentricity of hydrostatic bearings and the linearity of hydrostatic guides are better than that of the guide surfaces themselves.
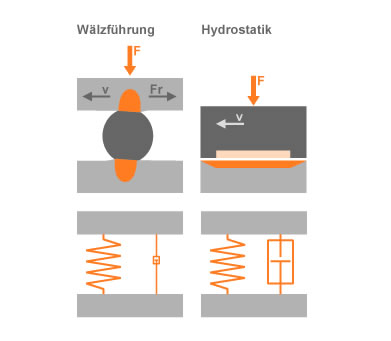
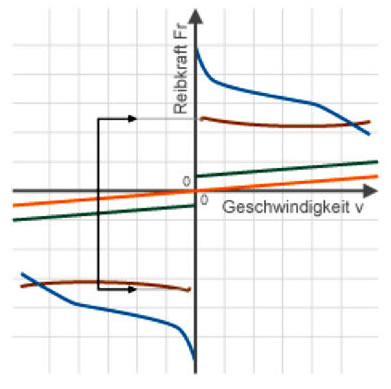
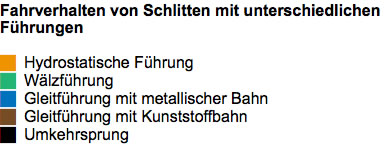
Advantages over sliding systems
Powers of ten - better damping
Your advantage:
- higher quality of the workpiece surface
- higher tool life and
- higher limiting cutting performance
Wear-free
Your advantages:
- Machine characteristics independent of service life
- greater availability of the machines
- lower maintenance costs
- longer machine life and
- lower annual machine costs
Speed or speed-independent properties
Your advantages:
- higher workpiece accuracy
- speed-independent splitting heights
- speed-independent stiffness
In contrast to slideways and plain bearings, hydrostatic guides and bearings are permanently free of backlash.
The friction of hydrostatic guides is powers of ten lower and proportional to the speed. In contrast to sliding guides, hydrostatics avoid a jump in force when the direction of movement is reversed and also the stick-slip effect.
several times higher positioning accuracy and path fidelity of guideways, especially when reversing the direction of motion,
- Higher travel speeds or peripheral speeds possible
Very low friction of high-speed bearing arrangements
Your advantages:
- higher possible speeds
- lower heat input
The frictional heat generated in high-speed bearings is better dissipated from the machine
The machine can be tempered by supplying cooled oil. Your advantages:
- Better thermal stability of the machine
Reduced sensitivity to soiling
As contamination in hydrostatic systems is mainly flushed out by oil and not rolled into the raceways as is the case with rolling bearings and guides, this leads to. Your advantages:
- Greater functional reliability
- Machine properties independent of service life
- Greater availability of machines
- lower maintenance costs and
- longer machine service life and
- Lower annual machine costs
Shape errors in the guide surfaces are largely compensated for by the hydrostatic system
- The concentricity of hydrostatic bearings and the linearity of hydrostatic guideways are better than that of the guide surfaces themselves.
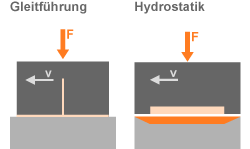
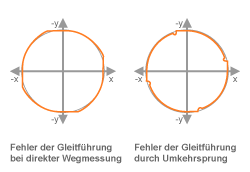
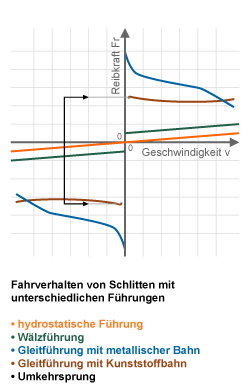
ADVANTAGES OVER NORMAL HYDROSTATICS with capillaries
General advantages of PM controllers
- 4-5 times stiffness with comparable data,
- significantly reduced oil requirement,
- lower necessary pump pressure due to the high utilization of the pump pressure,
- significantly smaller necessary pump and motor power
- Adjustment of stiffness by different preload for wrap-around solutions.
Advantages of using PM controllers on guideways
- Often, a wrap can be omitted if the load directions allow it, since with PM controllers the wrap is often not necessary only to increase the stiffness.
- In the case of guides without a handle, the stiffness can additionally be significantly increased by vacuum pockets.
- On guideways with a handle, the stiffness of the guideway can be adjusted largely independently of the load capacity by varying the preload.
Advantages of using PM controllers on high-speed bearing arrangements
- several times lower power dissipation,
- significantly higher maximum speed,
- higher stiffness and damping,
- high-speed spindle bearings can also be subjected to high loads,
- higher functional reliability.
Advantages of using PM controllers on screw drives
- It is only by using our PM regulators instead of capillaries that stiffnesses equal to or better than those of ball screws can be achieved, although the size of the pocket areas is limited. PM controllers are therefore a prerequisite for the production of functional hydrostatic lead screws.
- High axial loads are possible, as up to 80% of the pump pressure acts as differential pressure with PM regulators in bypass solutions.
Advantages of using PM controllers on high-speed bearing arrangements
- several times lower power dissipation,
- reduced displacement,
- higher functional reliability,
- significantly higher maximum speed,
- high-speed spindle bearings can also be subjected to high loads.
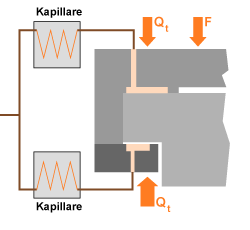
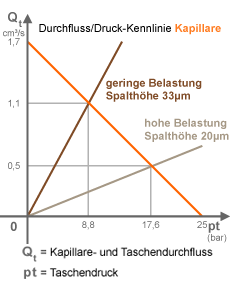
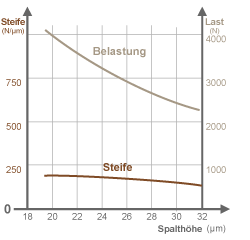
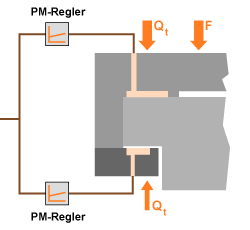
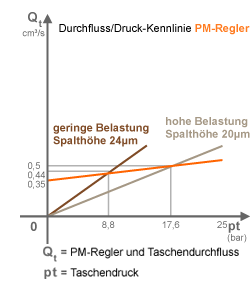
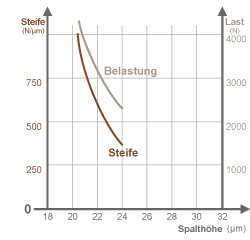